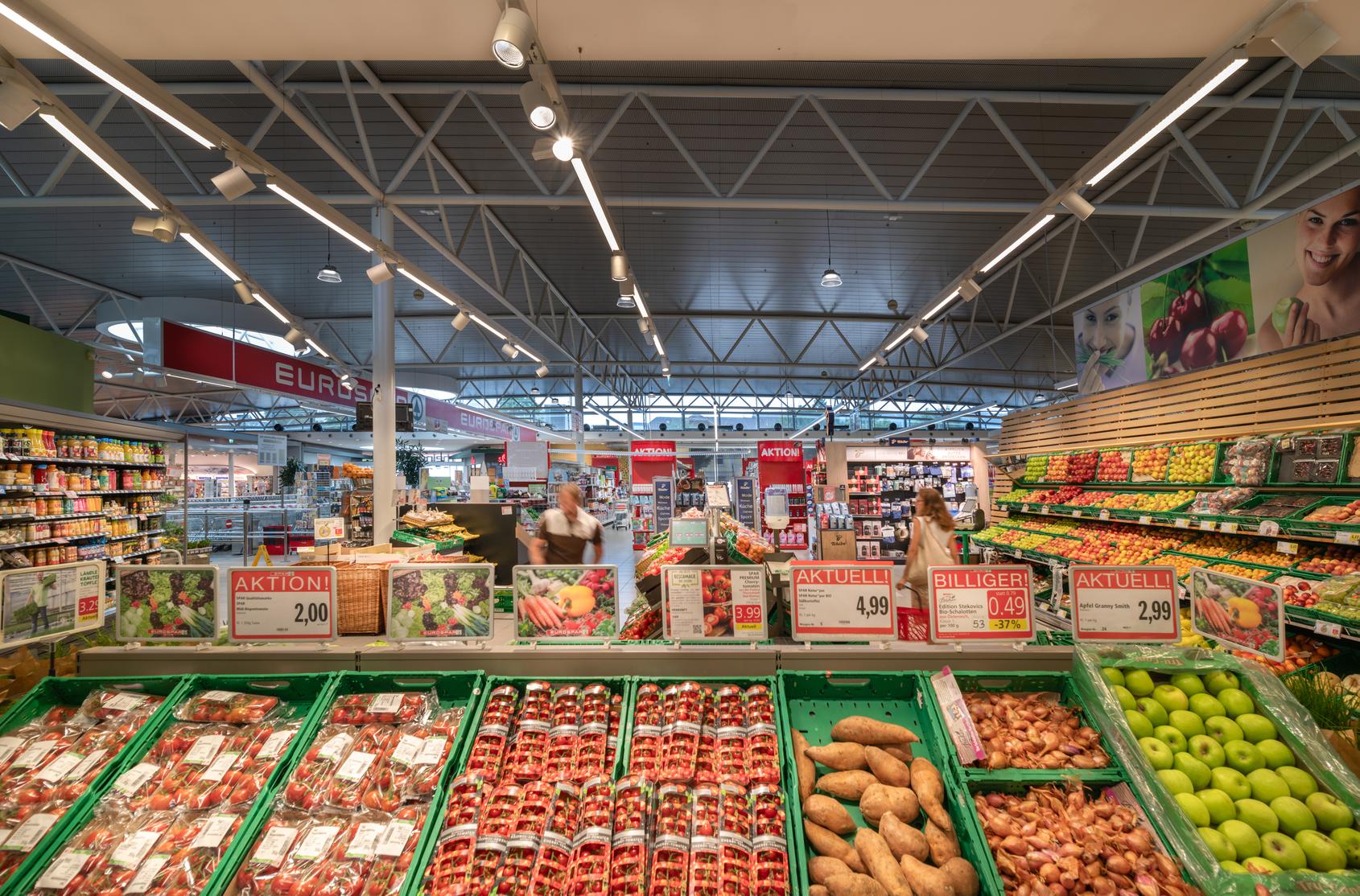
Zumtobel has worked with carla Vorarlberg, the Caritas social enterprise and voestalpine Stahl GmbH to achieve a circularity milestone. In a joint pilot project, the partners developed a scalable concept for the repair, reuse and high-value recycling of luminaires and trunking in the food retail sector using the example of the 449-metre-long TECTON continuous-row lighting system in the EUROSPAR shop at the Rheincenter Lustenau.
Refurbishment and the resulting use of more energy-efficient lighting is currently a hot topic in the retail sector, be it the switch to LED in the wake of the fluorescent tube ban or the upgrade to a newer generation of LED luminaires. However, there is still a long way to go in terms of sustainability when it comes to replacing old luminaires in supermarkets with more energy-efficient LED versions – at present, most of the obsolete lighting breaks during the dismantling process or is disposed of for other reasons. But these luminaires and lighting tracks are full of valuable raw materials such as steel, copper and aluminium. If recycled metals are used instead of primary raw materials in the production of new products, 48 percent of CO2 equivalents can be saved in the case of steel, for example. However, in order to close the product and material loops, a comprehensive plan for dismantling and material recycling is required.
Zumtobel has trialled a suitable process and value creation model for the repair, reuse, high-value recycling steps in a collaboration with social enterprise carla Vorarlberg and voestalpine Stahl GmbH. The model explores key aspects of circularity: How can luminaire systems be dismantled and transported carefully enough to ensure they can be used elsewhere? And how can the trunking materials reach the supplier without any loss of quality so they can be used as secondary raw materials for the next generation of luminaires?
Two loops for a more sustainable refurbishment process
Two loops were analysed as part of the project: those of the luminaires and of the tracks. Firstly, carla Vorarlberg examined the extent to which the dismantled TECTON luminaires could be reused at the company’s own premises. Secondly, it looked at recovering and separating the materials from the track system so the raw materials could be used in the production of new luminaires.
Key findings from the pilot project
At the EUROSPAR shop in the Rheincenter Lustenau, 449 metres of TECTON tracks were dismantled, separated or recycled. Over 72 kilograms of copper and 576 kilograms of steel were recovered from the track material as secondary raw materials, along with 91 kilograms of polypropylene from the 11-pole track guide. The findings were also particularly useful for modelling and scaling similar projects in the future.
The main challenge was to define efficient processes and quality standards for the dismantling, disassembly, collection, packaging and transport of the luminaires and to integrate these into the refurbishment process. Luminaires can only be reused if they are dismantled with care. Damage must be avoided, which requires an experienced and appropriately trained team. The well-organised collaboration between the electrical installation company Klampfer and carla Vorarlberg proved to be a significant factor in the pilot project’s success. The dismantled luminaires had to be checked for function and safety to ensure they could be reused. The individual technical and logistical steps, including packaging on site, had to be well planned and coordinated, particularly with the other teams on the construction site.
The luminaires from the pilot project were given a second life in the newly opened carla vintage store in Bregenz, where they create the perfect backdrop for the clothing and second-hand finds.
“The reuse of high-quality lamps in our new carla store in Bregenz shows how a loop can be closed in a very tangible way. This required collaboration between companies from very different sectors and of very different sizes – from listed companies to a regional social enterprise that employs people who are finding it particularly difficult to enter the labour market. For me, this openness to collaboration and joint learning is a hallmark of this pilot project and the key to solving the challenges in the circular economy,” says Karoline Mätzler, Head of Work & Qualifications, Caritas Vorarlberg.
“The excellent quality of the luminaires after years of use and the careful dismantling process was surprising and impressive – both their external condition and technical performance. Reuse as a circular solution is an ecologically and economically attractive option for the future. We look forward to working with our partners on further similar projects aimed at professionalising this process,” says Ines Göbel, Sustainability Manager at the Zumtobel Group.
Circularity a consideration as early as the design phase
The Zumtobel Group has been committed to circularity for many years, and it forms a central pillar of the company’s sustainability strategy. Inspired by the cradle-to-cradle approach, the internal Circular Design Rules (CDRs) are used as early as the product development stage to consider the subsequent return of the product and its parts to the material cycle. Launched in 2001, the TECTON track lighting system was already ahead of its time with regard to this approach. TECTON’s modular design, its ability to be dismantled and its use of high-quality, easily recyclable raw materials such as copper and steel make it the perfect object of investigation when it comes to circularity.